How Single Pair Ethernet Streamlines Industrial Networks
April 04, 2024
Blog
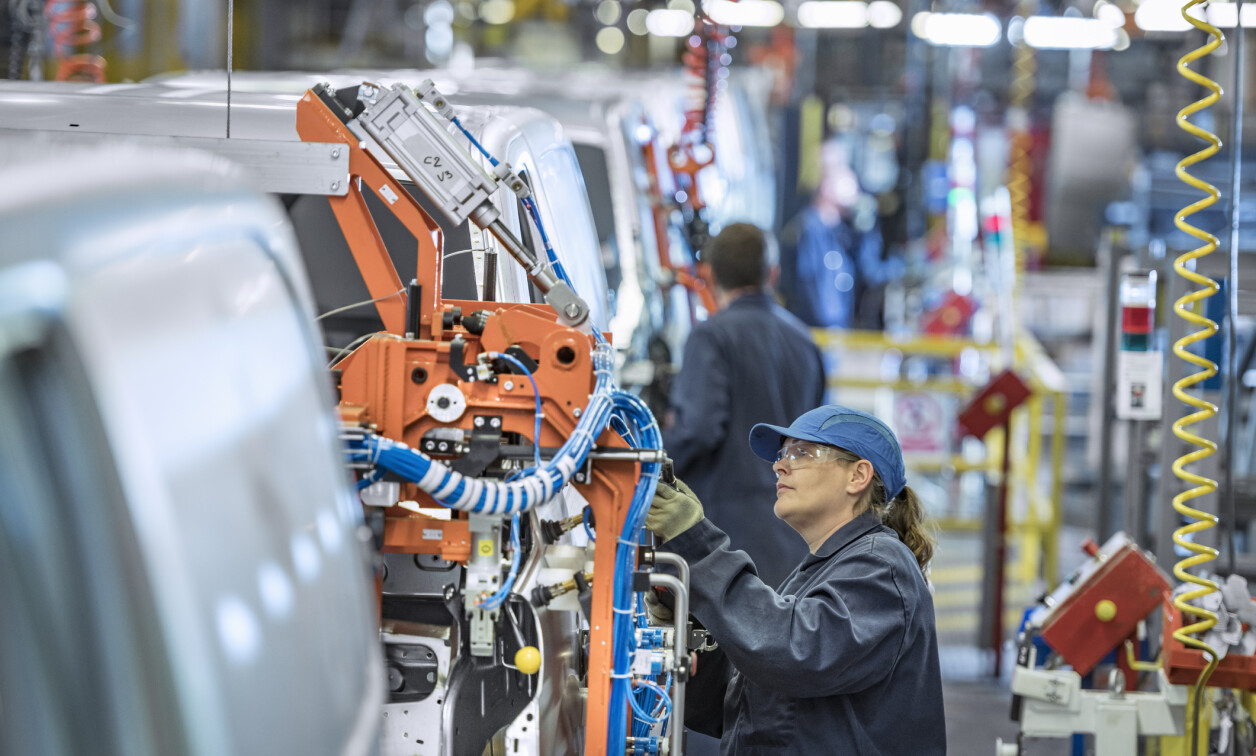
While retrofitting SPE into industrial plants is not going to happen overnight, the advantages of the technology are so compelling that there will likely be a gradual process of upgrading the networks over time.
As connectivity becomes increasingly important in all industries, there will be an increased demand to upgrade networks to support demand. The introduction and rapid adoption of Single Pair Ethernet (SPE) technology in the automotive industry is an example of one such method, and underscores the opportunity for this approach to expand to other industries, particularly those seeking options to cut network size, decrease complexity, increase efficiency and reliability, and improving workplace safety.
Traditionally, Ethernet networks have had four twisted wire pairs within their cables. In a drive to simplify things without compromising performance, the SPE standard was published in 2019 as IEEE 802.3cg.
It has long been possible to run an Ethernet connection over a single pair of wires, but it used to be difficult to use full duplex communication – simultaneous transmit and receive – over that single pair, so at least two pairs were needed.
As with so many advances in electronics, the evolving capabilities of semiconductors were the foundations of a breakthrough that made SPE practical and affordable. In this instance, it was the emergence of low power, low-cost devices with the processing power to execute echo-cancelling algorithms that prevent a network’s transmit and receive signals from colliding with each other.
Expanding from automotive to industrial applications
SPE technology gained immediate traction in the automotive industry, where size and weight savings reduce costs and help extend driving range – an important objective for electric vehicle makers. Now, the industrial IoT sector may be about to embrace the SPE too.
Industrial networks employ a variety of operational technology (OT) protocols including BACnet, RS-485, Modbus, Profinet, DeviceNet, MQTT, OPC, and Foundation Fieldbus. There is a lot of single-pair wiring already installed for OT networks and OEMs can now run SPE over the same connections, rather than having to build new physical networks with bulky and relatively inflexible multipair cables.
In terms of performance, SPE offers up to 1 Gbps data rate, a range of up to 1 km, and simultaneous delivery of up to 50 W of DC power over the same circuit with a maximum current rating of 1.36 A. This saves space, weight, and cost compared with having to run separate power feeds. As the power consumption of IoT sensors and other endpoints keeps falling, it means that many more devices can be powered over a single pair of wires, greatly simplifying network design and operation.
IEC 63171-C is the complementary SPE standardized connector form factor. The connectors are specified for various environmental conditions and take into account mechanical shock/vibration resistance, ingress protection, chemical resistance, and EMC compatibility. The specs are known as MICE levels. MICE 1 is equivalent to IP20 for office environments, MICE 2 for factories, and MICE 3 for the harshest industrial and outdoor conditions. With suitable housings, these connectors can achieve environmental ratings up to IP67.
What SPE means for industrial IoT networks
In industrial automation and control, networks can be streamlined and greatly simplified with SPE. This applies to both peer-to-peer networking and shared access through 10 Mbps multidrop technology where SPE is used as a backbone.
Multidrop employs PHY-level, Carrier Sense Multiple Access with Collision Detect (CSMACD). This means that before a node transmits, it checks if another carrier is present. If it is, it delays its next transmission for a randomly chosen period before checking again to see if any nodes have a carrier present and are transmitting. Network latency can still cause collisions but by stopping transmission immediately after a collision is detected, the time required before a retry is reduced and this minimizes latency.
For both types of networks, SPE offers lighter (60% less weight than a typical 4-pair cable), more flexible cabling with high bandwidth and robust EMI performance.
The Ethernet Alliance developed Single Pair Ethernet. Its popularity in the Industrial IoT is growing rapidly (Source: The Ethernet Alliance)
Installation and maintenance are made simpler with SPE, not least because anything designed for Ethernet can be run over a single pair. The need for protocol translation, and industrial gateways and hubs, can be avoided. What is more, the skills needed to operate and maintain the network are more widely accessible because more engineers are familiar with Ethernet than with all the myriad OT protocols that characterize legacy industrial networks.
SPE + TSN = Time-critical performance
Industrial (and automotive) applications often include a requirement for real-time or time-sensitive control. Cobots, AI-driven sensors, and fast cycle-time actuators such as servo motors typically demand this, so assured synchronized networking is needed, and latency must be tightly controlled.
In November 2012, the IEEE’s time-sensitive networking (TSN) task group was established. The group’s goal was to create a standard for deterministic and predictable timing behaviour in Ethernet networks. Their efforts resulted in the publication of additions to IEEE 802.1 (mostly to IEEE 802.1Q Bridges and Bridged Networks) which define TSN profiles for synchronization, latency, reliability, and resource management. It applies to all Ethernet standards, including SPE, and these protocols can be implemented alongside non-deterministic network traffic for those applications that require determinism.
While retrofitting SPE into industrial plants is not going to happen overnight, the advantages of the technology are so compelling that there will likely be a gradual process of upgrading the networks over time. For new facilities, using SPE will cut network size, CAPEX and OPEX, complexity, and weight. At the same time, the technology will drive production efficiency, deliver greater network reliability, and help maintain safer working environments.